Company Milestones
2000
2000
Invention of ConXR 200 System
2004
First ConXR 200 Structure
210,943 ft2 Assembled in 21 Days
2007
Invention of ConXL 400 System
[bold_timeline_item_button title=”Expand” style=”” shape=”” color=”” size=”inline” url=”#” el_class=”bold_timeline_group_button”]
2008
2008
First ConXL 400 Structure
148,000 ft2 erected in 14 days
[bold_timeline_item_button title=”Expand” style=”” shape=”” color=”” size=”inline” url=”#” el_class=”bold_timeline_group_button”]
2009
2009
Completion of Full-Scale Bi-Axial Test Frame
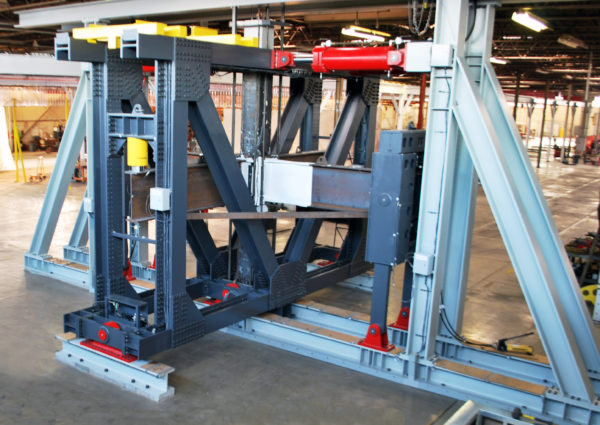
ConXtech’s unique Bi-Axial Test Frame tests full-scale ConX connections in both directions simultaneously.
[bold_timeline_item_button title=”Expand” style=”” shape=”” color=”” size=”inline” url=”#” el_class=”bold_timeline_group_button”]
2010
2010
Pre-qualified by HCAI/OSHPD for California hospitals
2010
First medical office for Kaiser Permanente
[bold_timeline_item_button title=”Expand” style=”” shape=”” color=”” size=”inline” url=”#” el_class=”bold_timeline_group_button”]
2011
2011
First Data Center
2011
ConXL formally codified in AISC 358-10;
design guide published as Chapter 10
[bold_timeline_item_button title=”Expand” style=”” shape=”” color=”” size=”inline” url=”#” el_class=”bold_timeline_group_button”]
2012
2012
First HCAI/OSHPD Project Erected
2012
First Industrial Pipe Rack Project
2012
First ConX Certified Fabricator & Erector
2013
ConX Systems are Cradle to Cradle Certified™
2013
First DSA Project Erected
2014
Company Expansion to Pleasanton, CA
[bold_timeline_item_button title=”Expand” style=”” shape=”” color=”” size=”inline” url=”#” el_class=”bold_timeline_group_button”]
2017
2017
First Two International Certified Fabricators
2017
10 Million ft2 delivered
2019
Grand Opening of ConXtech, Woodland, CA
2020
Executed Global Partnership Program
2020
2 Million sqft. of Kaiser Permanente Erected
[bold_timeline_item_button title=”Expand” style=”” shape=”” color=”” size=”inline” url=”#” el_class=”bold_timeline_group_button”]
2021
2021
New HQ in Pleasanton, CA
[bold_timeline_item_button title=”Expand” style=”” shape=”” color=”” size=”inline” url=”#” el_class=”bold_timeline_group_button”]
2022
2024
2024
Celebrating 20 innovative years!
ConXtech has been a pillar of progress for the past two decades in the ever-evolving world of structural steel construction.
2024
Falcon Brace Frame Invented
Drawing on decades of experience and cutting-edge technology, this new multipurpose gravity connection redefines structural integrity, efficiency and speed. These patented lower + locking gravity connections facilitate steel erection 3-5x faster than traditional forms of steel erection.
2024
35+ MOB’s Erected For Kaiser Permanente
[bold_timeline_item_button title=”Expand” style=”” shape=”” color=”” size=”inline” url=”#” el_class=”bold_timeline_group_button”]
2025
2025
20 Million ft2 delivered
[bold_timeline_item_button title=”Expand” style=”” shape=”” color=”” size=”inline” url=”#” el_class=”bold_timeline_group_button”]